“原來上一口甑要3個人,通過導入‘武漢造’
智能機器人自動上甑系統(tǒng),現在一個
機器人管3口甑,減少9人,一天3班倒,就是27人。”1月15日,在武漢市今年第二場智能化改造推廣會上,黃鶴樓酒業(yè)有限公司(以下簡稱黃鶴樓酒業(yè))黨委委員、總經理助理魏國介紹,公司全新的
智能化生產線已經改造升級完畢。
黃鶴樓智能化工廠使用
智能化改造后,新導入“武漢奮進”
智能機器人自動上甑系統(tǒng),產量翻一倍。
華中最大自動化單體釀酒車間年內建成
中國釀酒歷史源遠流長,東漢賈逵撰寫的《酒令》、曹操撰寫的《上九醞酒法奏》以及北魏賈思勰撰寫的《齊民要術》等,記載了數十種酒的制作方法。數字化時代,傳統(tǒng)酒廠如何謀劃智能化轉型,黃鶴樓酒業(yè)給出了自己的答案。
黃鶴樓酒是武漢乃至湖北歷史最悠久的白酒品牌之一,2011年,被國家商務部認定為“中國老字號”。2019年,黃鶴樓酒業(yè)武漢廠區(qū)獲批為首批湖北省傳統(tǒng)行業(yè)智能化改造示范項目。
1月15日,記者現場看到,相比于忙碌運轉的機器,偌大的黃鶴樓酒業(yè)釀酒車間,已經難覓工人的身影。選糧、潤糧、蒸糧、上甑、發(fā)酵、蒸餾等原來需要人工完成的工作,全部由機器人來完成。
熱氣蒸騰的潤糧區(qū),只見糧食,不見工人。潤糧又稱潤料,原本是釀酒工藝中最耗費人力的環(huán)節(jié)之一,黃鶴樓酒業(yè)導入自動化潤糧設備后,實現了自動拌料、智能潤糧的標準化作業(yè)。“原來需要4~6人翻料潤糧,現只需1人完成,潤糧效率和潤糧質量提升約45%。”該公司生產管理中心總監(jiān)陳彥龍說。
據陳彥龍介紹,通過持續(xù)升級自動化釀酒車間,公司實現了釀酒自動化,生產效率大大提升。他舉例,釀酒車間延續(xù)古法工藝,通過
自動化設備導入淘汰老舊生產力,整體效率提升約50%以上;包裝車間通過導入機器人自動化碼垛,碼垛效率提升約20%以上。
智能化改造,帶來的不只是產量的提升,還有安全隱患等方面風險的降低。
毗鄰釀酒車間的
智能制造管理控制中心,是黃鶴樓酒業(yè)的“中樞系統(tǒng)”,該中心的信息平臺,聯(lián)通生產運營過程中的生產、質量、設備、供應、倉儲、安全等諸多環(huán)節(jié)。
“實時監(jiān)控,一有異常立刻反應。”陳彥龍介紹,“信息平臺導入數據互聯(lián)互通,調度、生產執(zhí)行和倉儲等作業(yè)效率提升約20%以上。”
據了解,黃鶴樓酒業(yè)目前擁有武漢、咸寧、隨州三大廠區(qū)。武漢廠區(qū)生產線的改造只是黃鶴樓酒業(yè)
智能化升級的第一步,目前,隨州廠區(qū)將在今年建成華中區(qū)域最大的釀酒車間,生產線均采用自動化設備,“全部上的智能化設備,光設備就投了3個多億”。
釀酒機器人,武漢造
在黃鶴樓酒業(yè)釀酒車間,一臺巨大的自動裝甑摘酒的機器人引人注目,上面的“奮進”二字,清晰的顯示了這是一臺“武漢造”
機器人。
近年來,包括黃鶴樓酒業(yè)在內,多家酒企相繼宣布技改計劃,加快擴大生產能力、智能化系統(tǒng)更新改造,而在這些傳統(tǒng)酒企智能化轉型背后,來自武漢的奮進智能機器有限公司(以下簡稱“武漢奮進智能”)功不可沒。
成立于2014年的武漢奮進智能,主要服務于釀造自動化和電力作業(yè)安全兩大領域。該公司大區(qū)域總監(jiān)艾華亭介紹,公司全球首創(chuàng)的上甑機器人已經在茅臺、洋河等30多家知名酒企成功
應用,全國市場占有率超過90%。
上甑,是白酒釀造的一道核心工序,往往需要工作多年的老師傅憑借經驗操作,才能保證酒的質量和產量。2016年,針對白酒釀造這個關鍵環(huán)節(jié),武漢奮進智能向定制機器人轉型,制造
上甑機器人,并迅速成為這個細分賽道的領跑者。2018年召開的第三屆世界機器人大會上,武漢奮進智能的“上甑機器人”技術,被工信部作為先進案例推介。
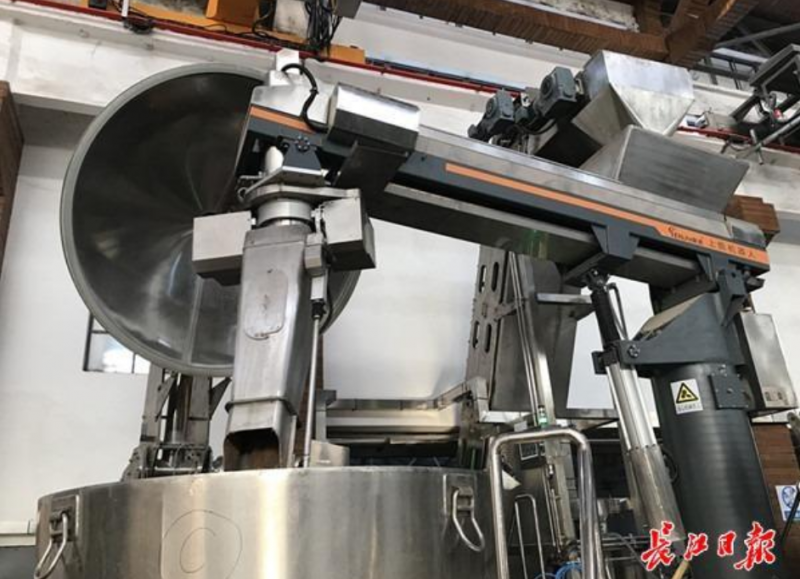
自動化機器人。
針對白酒釀造行業(yè)的痛點,武漢奮進智能還在研發(fā)摘酒機器人、出入窖機器人等,“3至5年內,專注于提供白酒智慧釀造解決方案,致力于成為白酒釀造領域先進制造技術的引領者和領導者。”艾華亭說。
據了解,截至目前,黃鶴樓酒業(yè)已與武漢奮進達成了30臺機器人的采購意向。“作為武漢的企業(yè),我們要對‘武漢造’品牌加大支持力度。”魏國說。
“企業(yè)
智能化改造是解決當前卡脖子、補短板的重要舉措,希望線上線下企業(yè)能夠抓住機遇,助力武漢智能化改造再上臺階。”市經信局相關負責人會上表示。
據介紹,截至目前,武漢市已連續(xù)舉辦了30場工業(yè)企業(yè)
智能化改造示范項目推廣會,咨詢診斷規(guī)模以上工業(yè)企業(yè)616家,智能化改造立項項目數285項,建設了一批有影響力的數字車間、智能工廠標桿。(記者李琴 賀亮 陳潔 通訊員武經宣)